CNC Router: Difference between revisions
(46 intermediate revisions by 5 users not shown) | |||
Line 1: | Line 1: | ||
[[File: | {{Equipment | ||
| title = CNC Router | |||
| image = IMG_20160216_231457.jpg | |||
| owner = Hackspace | |||
| induction = Yes | |||
| rfid = No | |||
}}==Specifications== | |||
* 800 W water cooled spindle 220 V 6.5 A with ER11 collet | |||
* 1.5 kw VFD capable of 3000-23000 rpm | |||
* 3.2 Nm NEMA 23 steppers | |||
* 36 V Stepper power supply | |||
* 2.5 A Stepper drivers | |||
* 325 mm x 250 mm x 100mm workspace | |||
* No load max feed of 5000mm/min | |||
* 6 x Capacitive 6-36V end stops | |||
==Induction== | |||
[[File:Cnc-router-fixturing-anno.png|thumb|alt=Expected ficturing of workpiece|Expected fixturing of workpiece]] | |||
[[File:Cnc-router-induction-toolbits.jpg|thumb|alt=Tools you will be using|Tools you will be using]] | |||
You are required to undertake an induction before using this machine, which will cover the basics of workholding and running the machine. This will teach you how to set up and home the machine, change tools and run programs using the LinuxCNC software. There is a charge for the induction to cover the cost of materials. | |||
Use the DXF file located on the [http://bit.ly/2lJUcv1 Google Drive] to work from. You will also find a detailed drawing illustrating the dimensions you should be working to, and a render to give you an idea of what you are heading towards. | |||
The software you use to generate the G-code is up to you. If you are on Windows or Mac I recommend Fusion 360. It's free (as in beer) and there are some fantastic video tutorials on YouTube to get you started, and the advantage is that the CAD modelling and CAM programming parts are integrated into one piece of software. Use the LinuxCNC Milling post-processor. | |||
If you are on Linux or some variation thereof, you'll have to work this out yourself I'm afraid. The free (as in speech) web-based CAM software [[http://www.makercam.com MakerCAM]] is relatively easy to use but a little limited. The downside is that it is built on Flash. I would strongly recommend staying away from Blender. Great for 3D modelling, not great for CAD. | |||
Please remember that this is a machine induction and not a CNC programming workshop. That will come at another time. | |||
* Rough stock provided is approximately 120 mm x 80 mm x 12 mm | |||
**Note: If using Fusion 360, you should set the origin of your material to the top surface and not the bottom (table) - this will avoid the cutter crashing through your material | |||
* Set Z 0 to be the top of the rough stock, it's easier this way. | |||
* Use either a 16 mm or a 12 mm diameter straight flute end mill to face the top surface to 10 mm thick. Leave room for clamping either end (about 5 mm top and bottom). Feed at 700 mm/min at a spindle speed of about 10,000 RPM. | |||
* Using the same end mill pocket the circular area 1 mm deep. Keep the feed and speed the same as above. | |||
* Use a 30 degree V-engraving bit to engrave the logo 0.5 mm deep. The tip of the engraving bit is 0.7 mm wide. Feed at 700 mm/min at 12,000 RPM. | |||
* Use a 6 mm straight flute end mill to route the two rectangular pockets and the profile. Keep tabs on the outside of the material to keep it in place after profiling. Two tabs at the top and two at the bottom (towards the clamps) should be good enough. Feed at 700 mm/min at a 12,000 RPM. Step down 2 mm at a time. | |||
The tools you will be using in this induction are located in the vicinity of the CNC router, look on the work top and also in the second drawer of the mini filing cabinet. | |||
==Using the Mill== | |||
You need an induction before you can use this machine. | |||
Reading this summary is not an induction, and is for reminder only. | |||
===Power-On Cycle=== | |||
[[File:cnc-router-mainpower.jpg|thumb|alt=Main Power push button|Main Power push button]] | |||
[[File:LinuxCNC-power-on-button.png|thumb|alt=LinuxCNC Power On Button|Power On Button]] | |||
* Turn on the power to the control box located underneath the router bed using the switch labelled ''Main Power'' | |||
* Turn on the controller PC. If the PC is already turned on, restart it - the control box needs to be on before the PC boots so that it can talk to the VFD correctly. | |||
* Release all of the CNC router's Emergency Stop buttons. | |||
* Once the PC has booted and loaded LinuxCNC click the ''Power'' button on the main interface, located in the top right. | |||
===Homing=== | |||
[[File:LinuxCNC-Before-After-Homing.png|thumb|alt=Before and After Homing|Before and after homing the machine.]] | |||
Every time the CNC router is turned on it needs to be homed. Homing moves all three axes to a known location so that the software can keep track of where it is. You will also have to re-home the machine after you have used the emergency stop or crashed into something. | |||
Until the machine has been homed the controller will not allow you to manually enter G-Code in MDI mode or run an NC program in Auto mode. | |||
[[File:LinuxCNC-home-buttons.png]] | |||
Homing functions are available on the home toolbar at the bottom of the screen. Click the first button to home all axes sequentially, or each of the other buttons to home an axis individually. The return button in the bottom right will take the toolbar back to the main screen. | |||
As the machine homes each axis the corresponding Digital Read Out (DRO) in the top right corner will change from red to green. | |||
===Jogging the machine=== | |||
[[File:LinuxCNC-Mill-Jogging-controls.png|thumb|alt=Jogging controls|Jogging controls]] | |||
Use the jogging controls to move the machine's axes. When moving the Y axis, think of it as if you are moving the spindle instead of the table. If you think that you are moving the table the jog directions will seems a bit odd. | |||
Clicking the hare icon will change it to a tortoise and it will put the machine into slow jogging mode - if you find that you can't jog around the table as fast as normal check that you aren't in tortoise mode. Additionally you can adjust the jog speed using the slider, the unit being millimetres per minute. | |||
The continuous mode is most useful for zipping around the work area, but as you get closer to the work and want to zero out it's quite helpful to change to one of the smaller options. Every time you press a key or button to jog it will move in discrete increments thus allowing you to sneak up on a dimension. | |||
== | Remember that the arrow keys on the keyboard also work to move in the X & Y dimensions, and Page Up and Page Down will move the Z axis. Pay particular attention when moving the Z-axis as it takes longer to move a similar distance and will often keep moving after you feel like it should have stopped. | ||
===Manual Data Input (MDI) mode=== | |||
It is much easier to move a machine precise amounts using G-Code. Once the machine has been homed you can access the MDI screen and enter G-Code to position the machine quickly and precisely, or even to perform quick one-off cuts. | |||
You need to understand basic G-code in order to use this machine, and this is the best place to check whether commands will do what you expect them to do. Be careful when entering commands, it's very easy to crash the machine. | |||
You might like to try moving the X axis to 0 as a 'rapid' movement using <code>G00 X0</code>, or performing a cut movement to Y axis position 10 at a rate of 250 mm/min with <code>G01 Y10 F250</code>. Starting the spindle at 8000 RPM is achieved using <code>M3 S8000</code> and changing the speed to 10,000 RPM is done by entering <code>S10000</code>. You can stop the spindle with <code>M5</code>. These are just examples, you really need to know basic g-code so that you can catch errors before they cause problems and ruin the machine or your work. | |||
We've done our best to set the machine so that it can't over-travel and wreck itself, but if you really abuse it you might run into problems, especially on the Z axis. | |||
==Configuration== | ==Configuration== | ||
The LinuxCNC configuration files are stored on [https://github.com/leedshackspace/cnc-router-config Github] for you to browse. Please don't edit anything on the machine without checking with someone else first. If you do make a change please submit a pull request. Ask if you are not sure how. | |||
===VFD=== | ===VFD=== | ||
The spindle is controlled by a [[VFD]]. The current configuration settings can be found on the [[VFD]] page. | The spindle is controlled by a Huanyang HY01D523B [[VFD]]. The current configuration settings can be found on the [[VFD]] page. | ||
===Drivers / Motors=== | ===Drivers / Motors=== | ||
Drivers are TB6600's capable of 50V 5A | Drivers are TB6600's 'capable' of 50V 5A | ||
*1/4 microstep mode | *1/4 microstep mode | ||
*Full power | *Full power | ||
Line 44: | Line 104: | ||
*Wired in series mode | *Wired in series mode | ||
*[[http://cnc4you.co.uk/resources/Stepper%20Motor%20Nema%2023%2060BYGH301B%203.1Nm.pdf Datasheet]] | *[[http://cnc4you.co.uk/resources/Stepper%20Motor%20Nema%2023%2060BYGH301B%203.1Nm.pdf Datasheet]] | ||
=== Build notes === | |||
The end stops are wired as follows: | |||
1 - Positive | |||
2 - Gnd | |||
3 - Signal | |||
4 - Signal | |||
Experimentation is required to determine which detector | |||
==Pledges== | ==Pledges== | ||
Line 82: | Line 153: | ||
* 36v 10A PSU (Aidan) | * 36v 10A PSU (Aidan) | ||
Parts needed | ===Parts needed=== | ||
* | * Cable chains (larger machine) | ||
* Regular stop / go button | * Regular stop / go button | ||
==Build== | ==Build log== | ||
*First cut occurred | *First cut occurred | ||
*Limit switches installed. | *Limit switches installed. | ||
Line 93: | Line 163: | ||
* Soft limits set (but broken!) | * Soft limits set (but broken!) | ||
*Dir inversion issues (0,0 should be lower left?) | *Dir inversion issues (0,0 should be lower left?) | ||
*Dir inversion worked out (its actually correct to set machine into negative space) | |||
*TB6600 Stepper Drivers Installed | |||
*Wasteboard installed | |||
*Some hold downs installed | |||
*Machine tightened and thread locked (blue) | |||
===Upcoming=== | |||
*Writing documentation | |||
*PWM spindle control / enable | |||
==Software Proposals== | ==Software Proposals== | ||
Line 99: | Line 178: | ||
CAM [http://www.cnc4everyone.com/software/cad-and-cam/] | CAM [http://www.cnc4everyone.com/software/cad-and-cam/] | ||
=== Hazards. === | |||
* 1) Chips in eyes. | |||
* 2) Hair or clothing caught in rotating parts. | |||
* 3) Cutting tool breaking or getting ejected from holder. | |||
* 4) Sharp objects and chips cutting fingers. | |||
* 5) Trip hazard from cables. | |||
* 6) Contact with cutter | |||
* 7) Fire | |||
* 8) Electrical shock | |||
* 9) Noise/ Dust | |||
=== Persons at risk. === | |||
* Operator. | |||
* Persons nearby. | |||
=== Initial assessment of risk. === | |||
{| class="wikitable" | |||
| Hazard identified || Severity || Probability || Risk Factor | |||
|- | |||
| Chips in eyes || style="text-align:right;" | 3 || style="text-align:right;" | 2 || style="text-align:right;" | 6 | |||
|- | |||
| Hair or clothes caught in rotating parts || style="text-align:right;" | 2 || style="text-align:right;" | 2 || style="text-align:right;" | 4 | |||
|- | |||
| Cutting tool breaking || style="text-align:right;" | 2 || style="text-align:right;" | 3 || style="text-align:right;" | 6 | |||
|- | |||
| Cuts from sharp objects || style="text-align:right;" | 1 || style="text-align:right;" | 3 || style="text-align:right;" | 3 | |||
|- | |||
| Trip Hazard from cables || style="text-align:right;" | 2 || style="text-align:right;" | 2 || style="text-align:right;" | 4 | |||
|- | |||
| Contact with Cutter || style="text-align:right;" | 3 || style="text-align:right;" | 2 || style="text-align:right;" | 6 | |||
|- | |||
| Fire || style="text-align:right;" | 4 || style="text-align:right;" | 2 || style="text-align:right;" | 8 | |||
|- | |||
| Electrical shock || style="text-align:right;" | 4 || style="text-align:right;" | 2 || style="text-align:right;" | 8 | |||
|- | |||
| Noise/ Dust || style="text-align:right;" | 2 || style="text-align:right;" | 3 || style="text-align:right;" | 6 | |||
|} | |||
=== Control measures. === | |||
* Users will be required to attend induction held by Aiden. | |||
* Safety glasses and ear defenders will be worn. | |||
* Check everything is secure before starting the motor and stand well back. | |||
* Users will be trained to mount the cutting tools and work pieces safely. | |||
* Always use a brush to clean away chips and swarf. | |||
* Operators to use lifting aids, or ask for assistance, when moving heavy objects. | |||
* Equipment will be checked for defects before each use to minimise the risk of possible electrical faults or fire. Carbon Dioxide extinguisher to be available for any electrical fires | |||
* The equipment will be checked before each use to ensure that there are no defects in the cable, casing or plug. | |||
* Cables to be kept clear of user and obstructions to prevent anyone from tripping over it | |||
=== Final assessment of risk === | |||
{| class="wikitable" | |||
| Hazard identified || Severity || Probability || Risk Factor | |||
|- | |||
| Chips in eyes || style="text-align:right;" | 3 || style="text-align:right;" | 1 || style="text-align:right;" | 3 | |||
|- | |||
| Hair or clothes caught in chuck || style="text-align:right;" | 3 || style="text-align:right;" | 1 || style="text-align:right;" | 3 | |||
|- | |||
| Cutting tool breaking || style="text-align:right;" | 2 || style="text-align:right;" | 1 || style="text-align:right;" | 2 | |||
|- | |||
| Cuts from sharp objects || style="text-align:right;" | 1 || style="text-align:right;" | 2 || style="text-align:right;" | 2 | |||
|- | |||
| Trip Hazard from cables || style="text-align:right;" | 2 || style="text-align:right;" | 1 || style="text-align:right;" | 2 | |||
|- | |||
| Contact with Cutter || style="text-align:right;" | 3 || style="text-align:right;" | 1 || style="text-align:right;" | 3 | |||
|- | |||
| Fire || style="text-align:right;" | 4 || style="text-align:right;" | 1 || style="text-align:right;" | 4 | |||
|- | |||
| Electrical shock || style="text-align:right;" | 4 || style="text-align:right;" | 1 || style="text-align:right;" | 4 | |||
|- | |||
| Noise/ Dust || style="text-align:right;" | 2 || style="text-align:right;" | 1 || style="text-align:right;" | 2 | |||
|} | |||
=== Points system === | |||
{| class="wikitable" | |||
| Hazard severity || Points Rating || Definition | |||
|- | |||
| Nil || 1 || Very minor injury, bruise, graze, no risk of disease. | |||
|- | |||
| Slight || 2 || Minor injury, which would allow the individual to continue work after first aid treatment on site or at a local surgery. The duration of the stoppage or treatment is such that the normal flow of work is not seriously interrupted. | |||
|- | |||
| Moderate || 3 || Temporary disability causing injury or disease capable of keeping an individual off work for three days or more and reportable under RIDDOR | |||
|- | |||
| High || 4 || Causing death, serious injury or permanent disability to an individual. | |||
|- | |||
| Very high || 5 || Causing multiple deaths and widespread destruction eg. fire, building collapse. | |||
|} | |||
{| class="wikitable" | |||
| Hazard likelihood || Points Rating || Definition | |||
|- | |||
| Remote possibility || 1 || There is really no risk present. Only under freak conditions could there be any possibility of an accident or illness. All reasonable precautions have been taken - This should be the normal state of the workplace. | |||
|- | |||
| Unlikely || 2 || This incident or illness might occur but the probability is low and the risk minimal. | |||
|- | |||
| Possible || 3 || The accident may occur if additional factors precipitate it, but it is unlikely to happen without them. | |||
|- | |||
| Highly likely || 4 || Will happen more often than not. Additional factors could precipitate an incident but it is still likely to happen without this additional factor. | |||
|- | |||
| Inevitable || 5 || If the work continues as it is, there is almost 100% certainty that an accident will happen, for example: | |||
A broken stair or broken rung on a ladder | |||
Bare, exposed electrical conductors | |||
Unstable stacks of heavy boxes | |||
|} | |||
{| class="wikitable" | |||
| Risk Rating Score || Definition || Action | |||
|- | |||
| 1 to 4 || Low || No action required | |||
|- | |||
| 5 to 9 || Moderate || Reduce risks if reasonably practicable | |||
|- | |||
| 10 to 15 || High Risk || Priority action to be undertaken | |||
|- | |||
| 16 to 25 || Unacceptable || Action must be taken IMMEDIATELY | |||
|} | |||
[[Category:Tools_and_Equipment]] |
Latest revision as of 12:51, 18 July 2017
![]() | |
Equipment Information | |
---|---|
Status | Unknown |
Manufacturer | Unknown |
Model | Unknown |
Hackspace Information | |
Induction Required | Yes |
Induction Information | Here |
Card RFID Enabled | No |
Owner | Hackspace |
Specifications
- 800 W water cooled spindle 220 V 6.5 A with ER11 collet
- 1.5 kw VFD capable of 3000-23000 rpm
- 3.2 Nm NEMA 23 steppers
- 36 V Stepper power supply
- 2.5 A Stepper drivers
- 325 mm x 250 mm x 100mm workspace
- No load max feed of 5000mm/min
- 6 x Capacitive 6-36V end stops
Induction
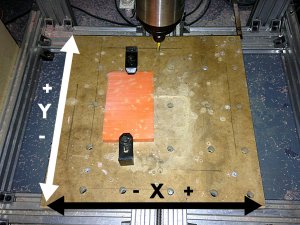
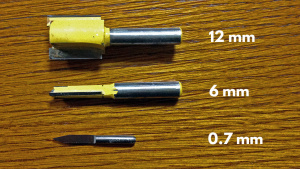
You are required to undertake an induction before using this machine, which will cover the basics of workholding and running the machine. This will teach you how to set up and home the machine, change tools and run programs using the LinuxCNC software. There is a charge for the induction to cover the cost of materials.
Use the DXF file located on the Google Drive to work from. You will also find a detailed drawing illustrating the dimensions you should be working to, and a render to give you an idea of what you are heading towards.
The software you use to generate the G-code is up to you. If you are on Windows or Mac I recommend Fusion 360. It's free (as in beer) and there are some fantastic video tutorials on YouTube to get you started, and the advantage is that the CAD modelling and CAM programming parts are integrated into one piece of software. Use the LinuxCNC Milling post-processor.
If you are on Linux or some variation thereof, you'll have to work this out yourself I'm afraid. The free (as in speech) web-based CAM software [MakerCAM] is relatively easy to use but a little limited. The downside is that it is built on Flash. I would strongly recommend staying away from Blender. Great for 3D modelling, not great for CAD.
Please remember that this is a machine induction and not a CNC programming workshop. That will come at another time.
- Rough stock provided is approximately 120 mm x 80 mm x 12 mm
- Note: If using Fusion 360, you should set the origin of your material to the top surface and not the bottom (table) - this will avoid the cutter crashing through your material
- Set Z 0 to be the top of the rough stock, it's easier this way.
- Use either a 16 mm or a 12 mm diameter straight flute end mill to face the top surface to 10 mm thick. Leave room for clamping either end (about 5 mm top and bottom). Feed at 700 mm/min at a spindle speed of about 10,000 RPM.
- Using the same end mill pocket the circular area 1 mm deep. Keep the feed and speed the same as above.
- Use a 30 degree V-engraving bit to engrave the logo 0.5 mm deep. The tip of the engraving bit is 0.7 mm wide. Feed at 700 mm/min at 12,000 RPM.
- Use a 6 mm straight flute end mill to route the two rectangular pockets and the profile. Keep tabs on the outside of the material to keep it in place after profiling. Two tabs at the top and two at the bottom (towards the clamps) should be good enough. Feed at 700 mm/min at a 12,000 RPM. Step down 2 mm at a time.
The tools you will be using in this induction are located in the vicinity of the CNC router, look on the work top and also in the second drawer of the mini filing cabinet.
Using the Mill
You need an induction before you can use this machine.
Reading this summary is not an induction, and is for reminder only.
Power-On Cycle

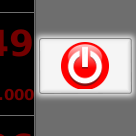
- Turn on the power to the control box located underneath the router bed using the switch labelled Main Power
- Turn on the controller PC. If the PC is already turned on, restart it - the control box needs to be on before the PC boots so that it can talk to the VFD correctly.
- Release all of the CNC router's Emergency Stop buttons.
- Once the PC has booted and loaded LinuxCNC click the Power button on the main interface, located in the top right.
Homing
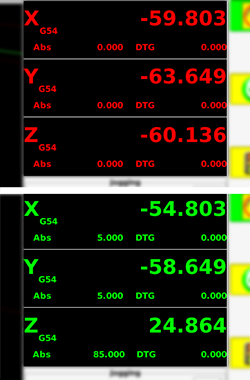
Every time the CNC router is turned on it needs to be homed. Homing moves all three axes to a known location so that the software can keep track of where it is. You will also have to re-home the machine after you have used the emergency stop or crashed into something.
Until the machine has been homed the controller will not allow you to manually enter G-Code in MDI mode or run an NC program in Auto mode.
Homing functions are available on the home toolbar at the bottom of the screen. Click the first button to home all axes sequentially, or each of the other buttons to home an axis individually. The return button in the bottom right will take the toolbar back to the main screen.
As the machine homes each axis the corresponding Digital Read Out (DRO) in the top right corner will change from red to green.
Jogging the machine
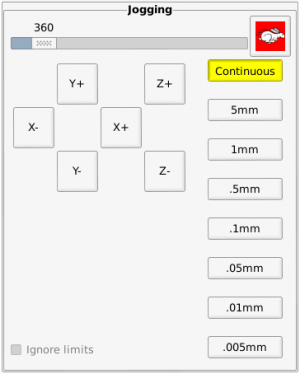
Use the jogging controls to move the machine's axes. When moving the Y axis, think of it as if you are moving the spindle instead of the table. If you think that you are moving the table the jog directions will seems a bit odd.
Clicking the hare icon will change it to a tortoise and it will put the machine into slow jogging mode - if you find that you can't jog around the table as fast as normal check that you aren't in tortoise mode. Additionally you can adjust the jog speed using the slider, the unit being millimetres per minute.
The continuous mode is most useful for zipping around the work area, but as you get closer to the work and want to zero out it's quite helpful to change to one of the smaller options. Every time you press a key or button to jog it will move in discrete increments thus allowing you to sneak up on a dimension.
Remember that the arrow keys on the keyboard also work to move in the X & Y dimensions, and Page Up and Page Down will move the Z axis. Pay particular attention when moving the Z-axis as it takes longer to move a similar distance and will often keep moving after you feel like it should have stopped.
Manual Data Input (MDI) mode
It is much easier to move a machine precise amounts using G-Code. Once the machine has been homed you can access the MDI screen and enter G-Code to position the machine quickly and precisely, or even to perform quick one-off cuts.
You need to understand basic G-code in order to use this machine, and this is the best place to check whether commands will do what you expect them to do. Be careful when entering commands, it's very easy to crash the machine.
You might like to try moving the X axis to 0 as a 'rapid' movement using G00 X0
, or performing a cut movement to Y axis position 10 at a rate of 250 mm/min with G01 Y10 F250
. Starting the spindle at 8000 RPM is achieved using M3 S8000
and changing the speed to 10,000 RPM is done by entering S10000
. You can stop the spindle with M5
. These are just examples, you really need to know basic g-code so that you can catch errors before they cause problems and ruin the machine or your work.
We've done our best to set the machine so that it can't over-travel and wreck itself, but if you really abuse it you might run into problems, especially on the Z axis.
Configuration
The LinuxCNC configuration files are stored on Github for you to browse. Please don't edit anything on the machine without checking with someone else first. If you do make a change please submit a pull request. Ask if you are not sure how.
VFD
The spindle is controlled by a Huanyang HY01D523B VFD. The current configuration settings can be found on the VFD page.
Drivers / Motors
Drivers are TB6600's 'capable' of 50V 5A
- 1/4 microstep mode
- Full power
- Supplied with 36V
Motors are 3.1Nm Nema 23
- Wired in series mode
- [Datasheet]
Build notes
The end stops are wired as follows:
1 - Positive 2 - Gnd 3 - Signal 4 - Signal
Experimentation is required to determine which detector
Pledges
A pledge tracker can be found on this google sheet [1]
Design
The first machine is a 'out of the box' C Beam Machine kit [2]. This is a X/Y table machine based on the C Beam aluminum profile which offers better stability and accuracy than OX type v slot or shapeoko.
This kit will be used to make the plates for its own upgrades into our specific 1000mm x 750mm gantry style machine with dual X drive based on this design. [3]
Parts Status
We have purchased the majority of parts from Colin at robocutters.co.uk[4], he offered a wealth of advice, a great discount and is genuinely interested in supporting Hackspaces.
- A C Beam machine kit
- 3 NEMA 23 Motors
- 1 1000mm linear actuator kit
- 1 750mm linear actuator kit
- 4 750mm 60 aluminium profiles
- 16 wheel kits
From China we ordered as a kit:
- 800W 60mm mount water cooled spindle
- 1.5kW VFD
- 12 VPump
- Various collets
From other sources:
- 6 C.P type limit switches (swwils)
- Radiator (swwils)
- 4 Core spindle cable (swwils)
- RUMBA Board + Drivers (Martyn)
- E-stop (Aidan)
- Arduino CNC sheild (swwils)
- Arduino UNO (swwils)
- 36v 10A PSU (Aidan)
Parts needed
- Cable chains (larger machine)
- Regular stop / go button
Build log
- First cut occurred
- Limit switches installed.
- Hard limits set
- Soft limits set (but broken!)
- Dir inversion issues (0,0 should be lower left?)
- Dir inversion worked out (its actually correct to set machine into negative space)
- TB6600 Stepper Drivers Installed
- Wasteboard installed
- Some hold downs installed
- Machine tightened and thread locked (blue)
Upcoming
- Writing documentation
- PWM spindle control / enable
Software Proposals
GRBL vs TINYG [5]
CAM [6]
Hazards.
- 1) Chips in eyes.
- 2) Hair or clothing caught in rotating parts.
- 3) Cutting tool breaking or getting ejected from holder.
- 4) Sharp objects and chips cutting fingers.
- 5) Trip hazard from cables.
- 6) Contact with cutter
- 7) Fire
- 8) Electrical shock
- 9) Noise/ Dust
Persons at risk.
- Operator.
- Persons nearby.
Initial assessment of risk.
Hazard identified | Severity | Probability | Risk Factor |
Chips in eyes | 3 | 2 | 6 |
Hair or clothes caught in rotating parts | 2 | 2 | 4 |
Cutting tool breaking | 2 | 3 | 6 |
Cuts from sharp objects | 1 | 3 | 3 |
Trip Hazard from cables | 2 | 2 | 4 |
Contact with Cutter | 3 | 2 | 6 |
Fire | 4 | 2 | 8 |
Electrical shock | 4 | 2 | 8 |
Noise/ Dust | 2 | 3 | 6 |
Control measures.
- Users will be required to attend induction held by Aiden.
- Safety glasses and ear defenders will be worn.
- Check everything is secure before starting the motor and stand well back.
- Users will be trained to mount the cutting tools and work pieces safely.
- Always use a brush to clean away chips and swarf.
- Operators to use lifting aids, or ask for assistance, when moving heavy objects.
- Equipment will be checked for defects before each use to minimise the risk of possible electrical faults or fire. Carbon Dioxide extinguisher to be available for any electrical fires
- The equipment will be checked before each use to ensure that there are no defects in the cable, casing or plug.
- Cables to be kept clear of user and obstructions to prevent anyone from tripping over it
Final assessment of risk
Hazard identified | Severity | Probability | Risk Factor |
Chips in eyes | 3 | 1 | 3 |
Hair or clothes caught in chuck | 3 | 1 | 3 |
Cutting tool breaking | 2 | 1 | 2 |
Cuts from sharp objects | 1 | 2 | 2 |
Trip Hazard from cables | 2 | 1 | 2 |
Contact with Cutter | 3 | 1 | 3 |
Fire | 4 | 1 | 4 |
Electrical shock | 4 | 1 | 4 |
Noise/ Dust | 2 | 1 | 2 |
Points system
Hazard severity | Points Rating | Definition |
Nil | 1 | Very minor injury, bruise, graze, no risk of disease. |
Slight | 2 | Minor injury, which would allow the individual to continue work after first aid treatment on site or at a local surgery. The duration of the stoppage or treatment is such that the normal flow of work is not seriously interrupted. |
Moderate | 3 | Temporary disability causing injury or disease capable of keeping an individual off work for three days or more and reportable under RIDDOR |
High | 4 | Causing death, serious injury or permanent disability to an individual. |
Very high | 5 | Causing multiple deaths and widespread destruction eg. fire, building collapse. |
Hazard likelihood | Points Rating | Definition |
Remote possibility | 1 | There is really no risk present. Only under freak conditions could there be any possibility of an accident or illness. All reasonable precautions have been taken - This should be the normal state of the workplace. |
Unlikely | 2 | This incident or illness might occur but the probability is low and the risk minimal. |
Possible | 3 | The accident may occur if additional factors precipitate it, but it is unlikely to happen without them. |
Highly likely | 4 | Will happen more often than not. Additional factors could precipitate an incident but it is still likely to happen without this additional factor. |
Inevitable | 5 | If the work continues as it is, there is almost 100% certainty that an accident will happen, for example:
A broken stair or broken rung on a ladder Bare, exposed electrical conductors Unstable stacks of heavy boxes |
Risk Rating Score | Definition | Action |
1 to 4 | Low | No action required |
5 to 9 | Moderate | Reduce risks if reasonably practicable |
10 to 15 | High Risk | Priority action to be undertaken |
16 to 25 | Unacceptable | Action must be taken IMMEDIATELY |